Penoxal wird auch im Bereich der Gynäkologie eingesetzt. Starke Immunität ist ein großartiges Mittel gegen unerwünschte Mikroorganismen, die Vaginalmykosen verursachen, oder gegen HPV-Viren, die Genitalwarzen oder präkanzeröse Veränderungen im Gebärmutterhals verursachen.
Was ist Penoxal
- Nahrungsergänzungsmittel aus einem natürlichen Mikroorganismus
- Zählt zu den medizinischen Heilschwämmen
- Der Wirkstoff Biocol wird in einer patentierten, modernen biotechnologischen Produktion hergestellt
- Eine Reihe medizinischer Untersuchungen mit großer Menge an praktischen Benutzererfahrungen und einer Benutzergeschichte seit 1972 wurde durchgeführt
Penoxal ist ein natürliches Nahrungsergänzungsmittel mit positiver Wirkung auf das Immunsystem, das keine negativen oder toxischen Wirkungen zeigt. Es zeichnet sich durch die Fähigkeit aus, vor allem spezifische weiße Blutkörperchen – B- und T-Lymphozyten – zu unterstützten, die für eine korrekte Immunantwort und die Prävention von Krankheiten entscheidend sind. Seine ausgeprägte antioxidative Wirkung und seine Wirkung auf die Apoptose-Optimierung reduzieren das Risiko der Entstehung der schwersten gegenwärtigen Krankheit – Krebs. Penoxal trägt auch wesentlich zur Minderung der Nebenwirkungen von Chemotherapie und Strahlentherapie bei und führt die Blutwerte schneller auf den Normalwert zurück.
Neben einem positiven Effekt auf das Immunsystem hilft Penoxal bei der richtigen Funktion des Verdauungsapparats, in dem ein großer Teil unseres Immunsystems gespeichert ist. Durch die Regulierung des Säuregehalts der Magensäfte entlastet Penoxal von unangenehmen Sodbrennen und reduziert das Risiko von Magengeschwüren. Es unterstützt wünschenswert die Darmflora und reguliert die Entleerung (Verstopfung / Durchfall), was bei der Behandlung vieler Krankheiten verwendet werden kann, die zur Störung der Darmschleimhaut und damit zu einem erhöhten Risiko der Entstehung schwerer Erkrankungen führen. Mit positiven Auswirkungen auf die Verdauung trägt Penoxal zum richtigen Bauchgefühl und Gleichgewicht bei.
Durch die Harmonisierung einzelner Organsysteme ist Penoxal an der richtigen Funktion des Körpers und dem allgemeinen Wohlbefinden beteiligt.
Die Hauptbestandteile von Penoxal
Was Penoxal enthält und was es einzigartig macht
Biocol
Biocol ist eine einzigartige patentierte natürliche Substanz vom Produkt des Mikroorganismus talaromyces purpurogenus gewonnen wird.
Beta-glukan
Beta-Glucan ist ein natürlicher Stoff mit außergewöhnlicher Wirkung auf das Immunsystem.
Maltodextrin
Die hauptsächlich als bevorzugte Energiequelle in sportlichen Aktivitäten
Vitamin C
Vitamin C ist das bekannteste und am weitesten verbreiteten Vitamin, das für die Erhaltung der Gesundheit unerlässlich ist.
Wirkungen von Penoxal:
- Unterstützt die Immunität durch Stimulation der Menge und Aktivität von B- und T-Lymphozyten (weiße Blutkörperchen)
- wirkt als Antioxidans – schützt die Zellen vor oxidativem Stress und freien Radikalen
- lindert Nebenwirkungen der onkologischen Behandlung (Chemotherapie, Strahlentherapie)
- fördert das reibungslose Funktionieren des Verdauungstraktes, der Nieren, der Leber
- reduziert die unerwünschten Auswirkungen von RTG / UV-Strahlung
- normalisiert die Blutbildwerte
- bekämpft unerwünschte Mikroorganismen bei gynäkologischen und gastrointestinalen Erkrankungen
- trägt zur Entgiftung des Organismus bei
Indikation:
- bei der Behandlung onkologischer Erkrankungen (Chemotherapie, Strahlentherapie)
- Prävention von Krebsrezidiven
- Prävention von onkologischen Erkrankungen
- in präkanzerösen Bedingungen
- bei entzündlichen, viralen und bakteriellen Erkrankungen
- bei Erkrankungen des Verdauungstraktes
- bei gynäkologischen Erkrankungen
- im geschwächten Immunsystem
- in der prä- und postoperativen Behandlung
Nebenwirkungen:
Penoxal wird selbst bei hohen Dosierungen gut vertragen und erhöht nicht die Abhängigkeit von der Langzeitanwendung. Das Produkt hat keine Nebenwirkungen, es ist kein Antibiotikum, es ist völlig ungiftig und interagiert nicht mit anderen Produkten oder Medikamenten. In seltenen Fällen kann Durchfall auftreten. In diesem Fall empfehlen wir eine Senkung der Dosierung. Bei Autoimmunerkrankungen empfehlen wir Ihnen die Einnahme von Penoxal mit Ihrem Arzt zu konsultieren.
Mit hervorragenden Ergebnissen kann Penoxal zur Stärkung der Immunität bei Grippe und Erkältungen, entzündlichen, viralen und bakteriellen Erkrankungen sowie zur Vorbeugung eingesetzt werden.
Herstellung des Penoxal-Präparats
Die Produktion von Penoxal erfolgt in einer zertifizierten Produktionslinie mit den HACCP-Standards (System der Risikoanalyse und Feststellung der kritischen Kontrollpunkte). Die Eingangskontrolle der Rohstoffe wird hier angewandt, dies betrifft sowohl den Wirkstoff Biocol, als auch Vitamin C und Maltodextrin, oder die Gelatinekapseln. Alle Komponenten werden in einem genauen Verhältnis in einem Edelstahlbehälter vermischt und in die Maschine für die Produktion der Gelatinekapseln werden die Kapseln geschüttet. Die Linie ist automatisch und technologisch kontrolliert, alles ist selbst dosierend.
Vorbereitung der Rohstoffe
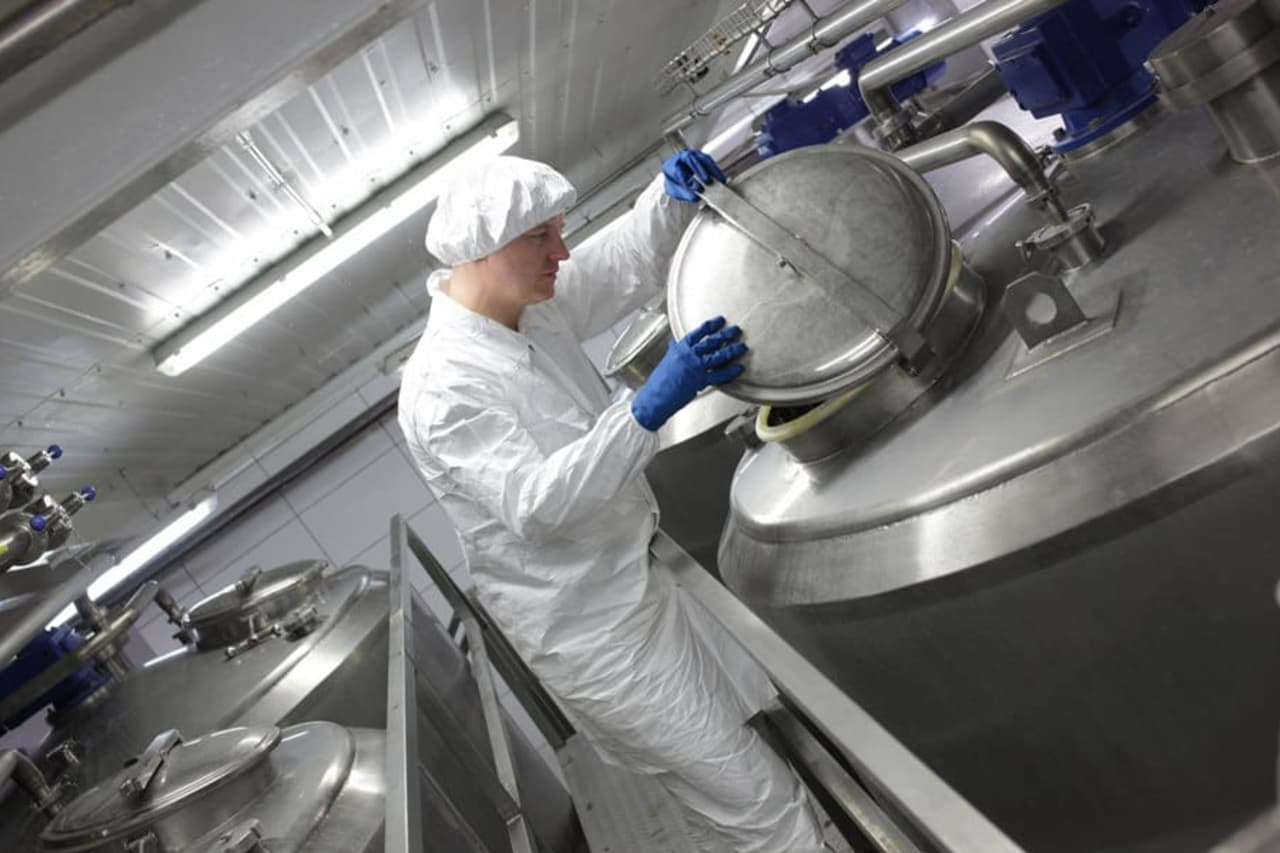
Fülllinie
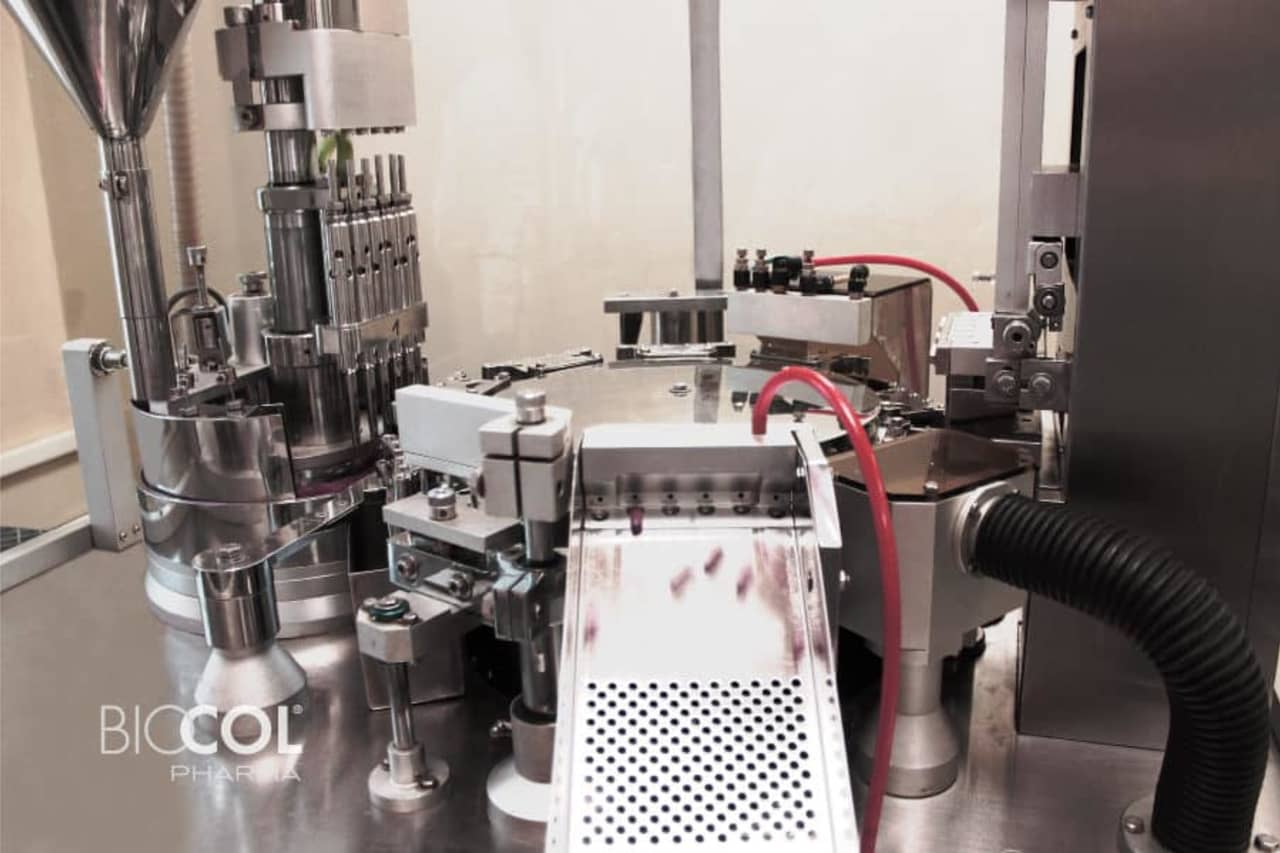
Verpackungslinie
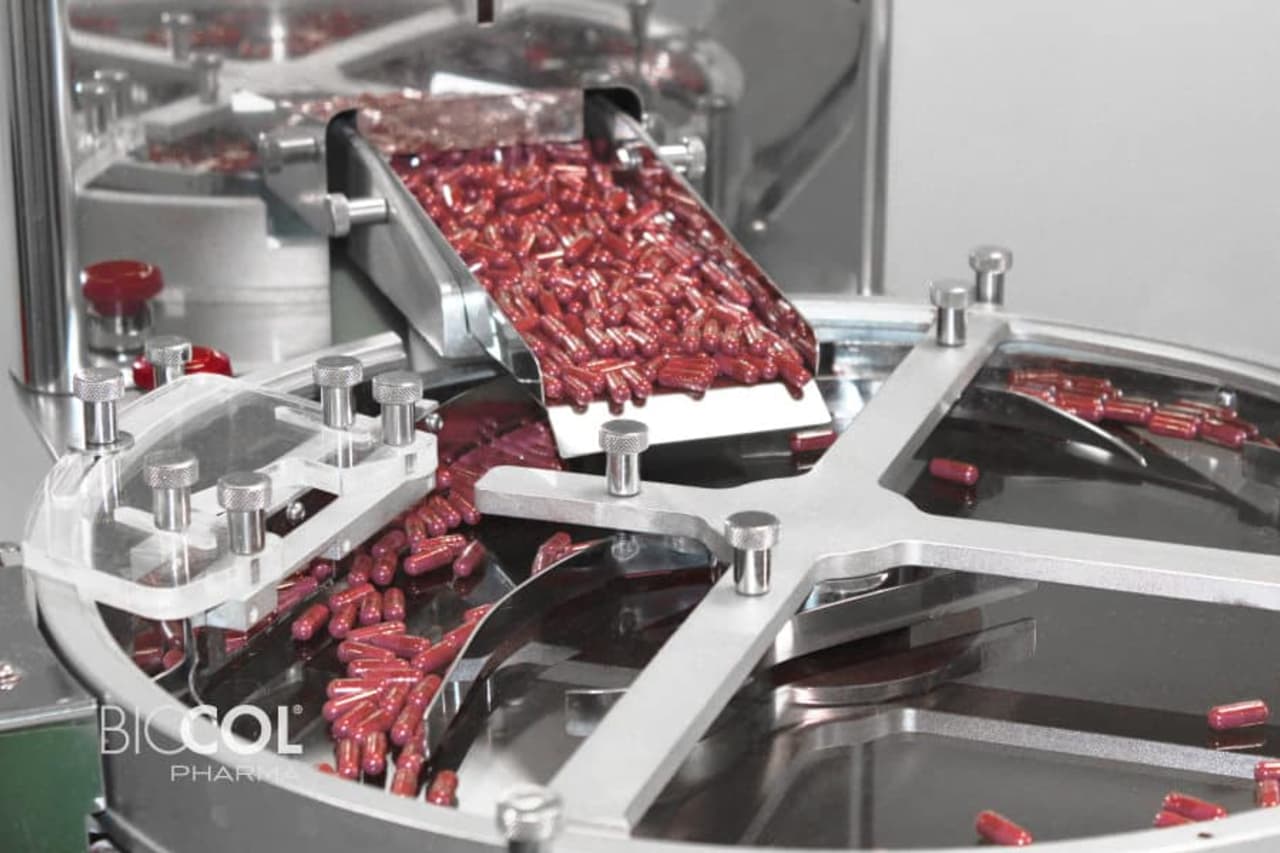
Die Kapseldosierung erfolgt maschinell und der Verschluss wird mit einem Sicherheitsring versiegelt. Die Ausgangskontrolle der fertigen Präparate führen 2 Arbeiter durch, sie kontrollieren den durchlaufenden Verlauf der Kapselproduktion und das, folgende Verpacken und Etikettieren. Das Verpacken in die Schachteln erfolgt durch eine halbautomatische Maschinenlinie, die die Schachteln zusammensetzt, und nach der Ergänzung des Beipackzetells wird die Schachtel geschlossen.
Der gesamte Prozess ist 100% sauber und genau. Im Verlauf des Füllens entnehmen die Arbeiter Stichproben, die sie wiegen und Laboruntersuchungen unterziehen Jede Probe, die mit einzelnen Chargen markiert wird, wird aufbewahrt.
Nach dem Befüllen der Kapsel wird die ganze Charge in die sog. Poliermaschine geschüttet, die sie von außen bürstet und den Staub absaugt, der sich beim Befüllen auf sie gelegt hat. Dann folgt das Befüllen der Behälter mit der Größe von 120 Kapseln, 60 Kapseln, eventuell Blister für die Packungen für 30 Kapseln.
Der gesamte Prozess läuft in einem geschlossenen Bereich unter strenger Qualitätskontrolle ab. Aus einer bestimmten Charge werden immer Proben entnommen, bei denen unabhängige Labors die Analyse der Gesundheitsunbedenklichkeit durchführen (mikrobiologische Reinheit und Schwermetalle). Nur hochwertige Produkte werden zum Verkauf angeboten.
Kontrolle der gesamten Produktion
Tests in unabhängigen Laboren
Bewertung von Penoxal
Guten Tag,ich heiße Rose und bin 63 Jahre alt. Letzten Sommer starb meine Mutter, mit der ich 40 Jahre unter…
Eine Geschichte lesen.Guten Tag,Im Dezember 2020 habe ich in meiner Brust einen Knoten ertastet, der Arzt hat mir versichert, es sei nichts,…
Eine Geschichte lesen.Ich habe mich lange nicht gut gefühlt und litt unter starken Blähungen und Wasserrückhaltung. Ich besuchte mehrmals meinen praktischen Arzt…
Eine Geschichte lesen.